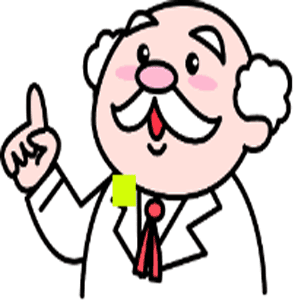
今回、実践的にPLCラダー回路の作成方法を紹介するにあたって、 まず、本記事の仕様書編とデバッ編は共通となっていますが、プログラミング編は2種類の方法グを紹介しています。
1.大体の人が作成している一般的なPLC回路の
・従来方式(本記事)
と、これを理解した上で、
2.弊社がおすすめするPLC回路である
・ステージ選択方式
と進んでそれぞれ参照して頂ければ、大容量のラダー回路もより簡単に作成することが可能と思います。
生産現場において、その機械設備がラインやラインの一部であっても、単体の設備であったとしても、必ず、半自動、全自動に限らず、シーケンス制御が使われています。
シーケンス制御には、主にリレーが使われますが、近年ではこれがPLCという制御機器にとって代ってきています。
電気設計者の作業概要!!
制御における”回路図”は、会社により“展開接続図”と呼ばれることも多くあります。
制御における回路図は、制御盤、操作盤、装置(M/C)に取付けの全ての電気に関する接続が書かれたものになります。
全ての部品に部品番号、全ての配線に線番号が割り振られ、回路図上にも、実部品、配線のも記載されています。
これにより、制御盤、操作盤、中継BOXなどの製作図、実態配線図や実機、及び盤間の配線図の設計が、可能となります。
また、加えて今後の検査やメンテナンスが可能となります。
PLCやパソコンが使われなかった時代のリレー(マグネットリレー)回路が主流だった頃は、数ページから数10、数100ページにも及ぶリレーシーケンス回路が描かれており、制御盤自体もかなり大型なものもありました。
しかしながら、シーケンス制御に"PLC"や"専用ボードコンピューター"、あるいは"パソコン"が使われるようになってからは、このリレーシーケンスの回路図の部分がほぼなくなることとなり、電源回路を除けば機器の接続図の様な形になることが多くなっています。
これらの場合、PLC使用時ではリレー回路と同じシーケンスをラダー図としてソフトウェアで記述し、またはパソコンや専用ボードコンピュータの使用時では、CやJAVA言語などで制御プログラムを作成するようになっています。
回路図作成準備
下記に、基本的な電気の設計における回路図について、図1~図6の回路図例を示し概要を説明していきます。
まず、電気回路設計者は、M/C(マシン)の動きや客先の要求、使用などを完全に理解する必要があります。
適当にすすめると後で変更が多発し、まともな回路図は出来ません。
まず、客先の仕様書を読んで理解する。
M/C(マシン)設計者、メカ設計者と打ち合わせを行い、M/Cの構造、動作を理解する。
動作タイムチャートをメカ設計者もらうか、ないならば、打ち合わせ後にこちら側から作って確認する。
まず、今回説明のターゲットのM/C(マシン・機械)は、下記の図1に示す様な外観で、アクチュエーター8往復(出ー戻り、前進-後退、上昇ー下降等々で 16動作)、それぞれの動作端位置検知(光電センサ)16個を使用したものを想定したものとします。
実際にどの様な手順で、設計を行い、プログラムを作成していくのでしょうか?
大きく分けて、下記の3項目となります。
1.仕様の確認・作成作業について(1/3 仕様書の作成編)
2.ラダー回路プログラムの作成について(2/3 プログラミング編)
3.実M/C(実機)で動かす前にラダー回路プログラムに間違いがないかを検証(3/3 デバッグ編)
本ページの『PLCラダー回路プログラムの作成1/3(仕様書の作成編)』では、仕様書の作成について、プログラムの作成前に最も重要な準備について具体例をあげて説明しています。
上記の仕様書の詳細検討や仕様をプログラムに必要な資料としてまとめるという作業は、時間もかかり、面倒なことからおろそかにする人が多いことが見受けられます。この時間が無駄だと考え、時間短縮としていきなりプログラムの作成作業を進めると後々様々な問題が発生し、仕様変更、また仕様変更の連続で、つぎはぎだらけのプログラムとなり、後に不具合が発生しても正確な理解が難しく、手に負えないものになりかねません。
PLCのラダー回路プログラムの作成に必要な仕様を詳細に決める
動作させるターゲットM/Cの装置外観(参考例)
今回制御したいM/C(ラインの一部だったり)を参考例として下記の様な外観とするとします。
【 図1】ターゲットM/C
機械設計者と打ち合わせを行い、機械の概要を知る。
1.外観
メカ設計の担当者は、機械の設計を行うときに、全体図という外観図面を作成し、ばらしの図面を作成し、各加工図面や部品を手配します。したがって、全体図をもとに、電気制御設計の担当者と打ち合わせを行うことが一般的です。
2.仕様
マシンの仕様、機能、特徴などの確認、また注意点も打ち合わせの中で聞いておきます
電気制御を含めたシステム構成全体について
どの様なアクチュエータを使用して、どの様なセンサーを使用するか
機械の動作タイムチャートについて
タイムチャートを提出してもらえばベストだが、意外と出ないので詳細を聞き出し、電気の設計者がまとめる場合も多い
設備の動作順序などの仕様決め、リスクアセスメントからセンサー、サーボ、制御盤位置、操作盤などの情報を知る
※リスクアセスメントとは、リスクの特定・分析・評価といった一連のプロセスである。
電気設計を担当する立場からボールネジや減速比のピッチ・ギア比を知り、モータ類もサーマルリレーやインバータの設定確認のための型式確認、センサーやソレノイドバルブ類の型式を確認します。
電気設計は、ハードウェア設計とソフトウェア設計に分類することができます。
ハードウェア設計
PLC周辺機器の選定と配線の設計を行う
電気回路図、電気制御部品の選定と部品表の作成、部品図・板金図作成、原価計算、制御盤や操作盤のレイアウト設計、ハーネス設計
ソフトウェア設計
ラダー言語にてPLCのシーケンス制御プログラムを作成を行う
シーケンス制御プログラム作成、画面ソフト(タッチパネル)の作成、デバイスマップ作成、サーボパラメータ調整、立ち上げ・デバッグ作業、操作説明書、操作指導
機械設計やハード設計は一度組立てが始まってしまうと変更が難しいですが、ソフトウェアには変更が容易と言う特徴があります。
そもそも変更が容易というのがPLCのメリットです。
だからといって、ハード面で発生した不具合を全てソフトで吸収できるものではありません。
詳細な仕様決め
詳細な仕様決めの手順を以下に示します。
システム構成の決定
上記の機械設計者との打ち合わせに基づき、電気制御の観点からシステム構成を作成します。
制御盤、操作盤、M/Cの内容(電磁弁、モーター、リミットセンサー)などの制御の全体構成を決定します。
【図2】 システム構成図
PLC入出力回路割付表の作成
制御に必要な各入出力をPLC端子のどこに割付けるかを決めます。
システム構成図に基づいて、PLC対する入出力割付表を作成する。
入力
制御に必要な各入力(操作盤取り付けの押し釦SWやM/C内の各アクチェーターの動作位置に取り付けされるリミットセンサーなど)をPLC入力端子のどこに割付けるかを決めます。( 例えばX000~X017に接続など)このX000~X017を記号としてこれから作成するラダープログラムで各入力の記号として使用していくことになります。もちろん、各記号は名称を決めることが出来ますので扱う上で同時に表示されます。
各入力を割り付けると下記の表の様になります。
【 図3】入力割付表
出力
制御に必要な各出力(操作盤等表示灯、及び空圧シリンダ(アクチュエータ)などに使用される電磁弁(ソレノイド)など)をPLC出力端子のどこに割付けるかを決めます。( 例えばY000~Y017に接続など)このY000~Y017を記号としてこれから作成するラダープログラムで各出力の記号として使用していくことになります。もちろん、各記号は名称を決めることが出来ますので扱う上で同時に表示されます。
各出力を割り付けると下記の表の様になります。
【 図4】入力割付表
自動運転動作の仕様決定
タイムチャートを提出してもらえばベストだが、意外と出ないので詳細を聞き出し、電気の設計者がまとめる場合も多い。
ラインの一部となるM/Cを含め、多くのM/Cは、スタート信号により自動運転を開始します。
この自動運転の仕様は、口頭や記憶ではなく、シーケンスタイムチャートなどで必ず図面化して仕様を明確に決定します。
この打ち合わせや取り決めがあらかじめしっかりまとめられているかどうかが、後の設計作業がスムーズに進むかどうかに大きくかかわります。もし、あいまいなまま作業が進められると多くの修正、重大なミスが発生し、しいてはプログラムも作成者ですら理解が難しい内容、バグの含んだ内容のものになってしまいかねません。
【 自動運転時動作タイムチャート】
【 図5】自動運転時動作タイムチャート(仕様書)